Despite the full-scale war, missile attacks on infrastructure and significant logistical challenges, Ukrainian steelmakers continue to implement their plans to decarbonize and improve the environmental performance of their operations. For example, Interpipe and Dnipro Metallurgical Plant recently presented their decarbonization strategies.
EcoPolitic decided to investigate the progress of domestic steel enterprises in this direction during full-scale invasion.
An important point to consider when assessing progress is that Ukrainian companies have to modernize their production at their own expense, without government support. In contrast, in the European Union, the decarbonization of industry, including steel sector, is supported by large-scale financial instruments such as the Just Transition Fund, the Innovation Fund, state aid mechanisms, grants, and concessional financing.
This allows European producers to implement green technologies faster and remain competitive in the global market in the face of new environmental requirements, including the Carbon Border Adjustment Mechanism (CBAM).
What are the achievements of Ukrainian steelmakers over more than 3 years of full-scale war? Let's take a closer look.
Interpipe
On May 16, this large company, a manufacturer of steel pipes and railway products, presented its Decarbonization Pathway. According to its data, in 2024, Interpipe's enterprises reduced CO2 emissions per ton of seamless pipe by 61% and railway products by 46% compared to 2010.
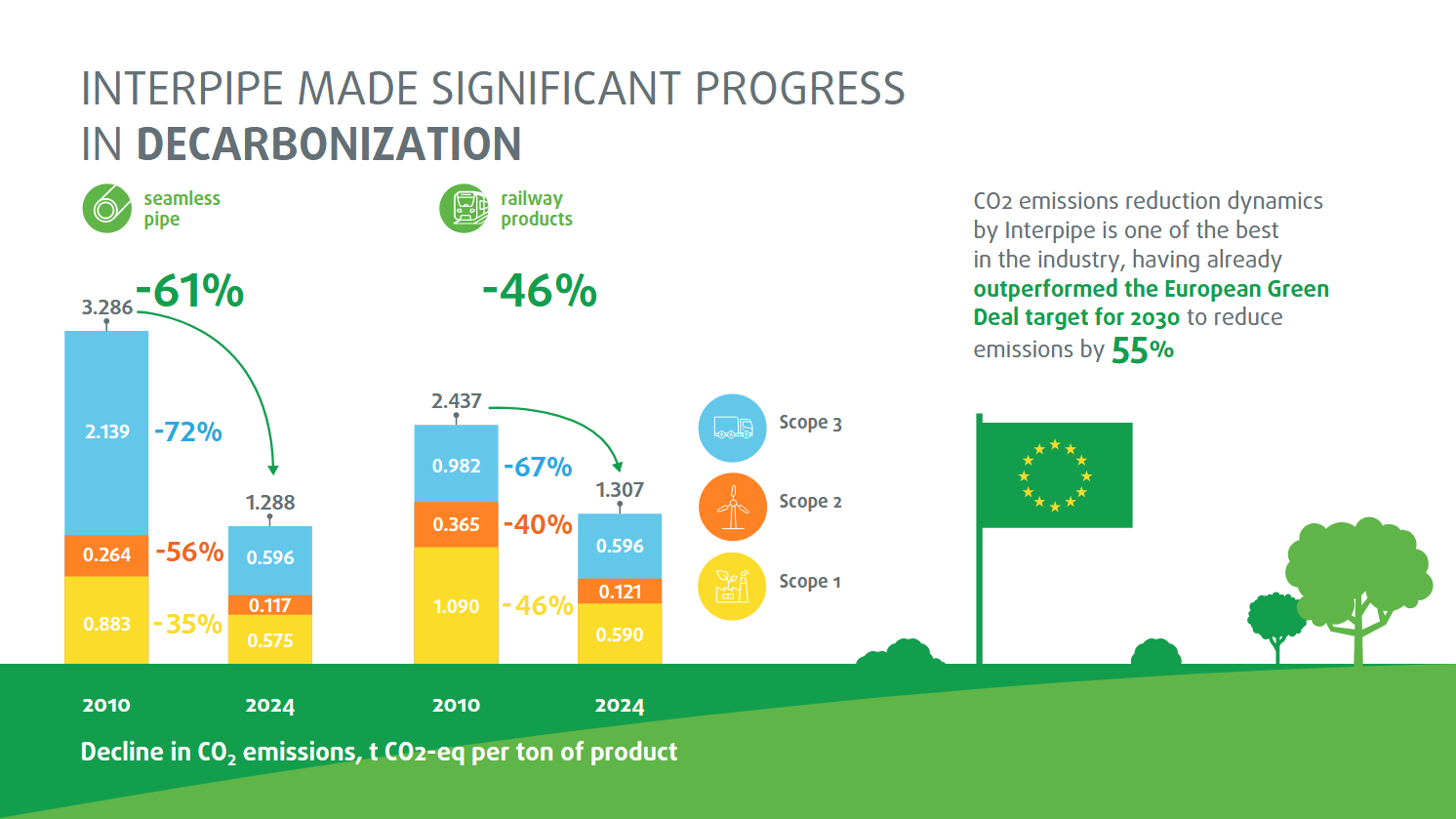
Source: interpipe.biz.
Such significant decarbonization figures were achieved mainly due to the modernization of steelmaking facilities. Back in 2012, the company launched an innovative electric steelmaking complex, Interpipe Steel, built from scratch. The company then invested $1 billion in this project and its related facilities. Interpipe says that this is the largest environmental investment in Ukrainian industry since the country's independence.
In 2024, the share of electricity from renewable energy sources (RES) reached 28% of the company's total electricity consumption. For comparison, in 2010, the share of green energy was 4 times less – only 7%. In general, the share of carbon-neutral electricity sources (nuclear + renewables) in Interpipe's total consumption last year was 64%.
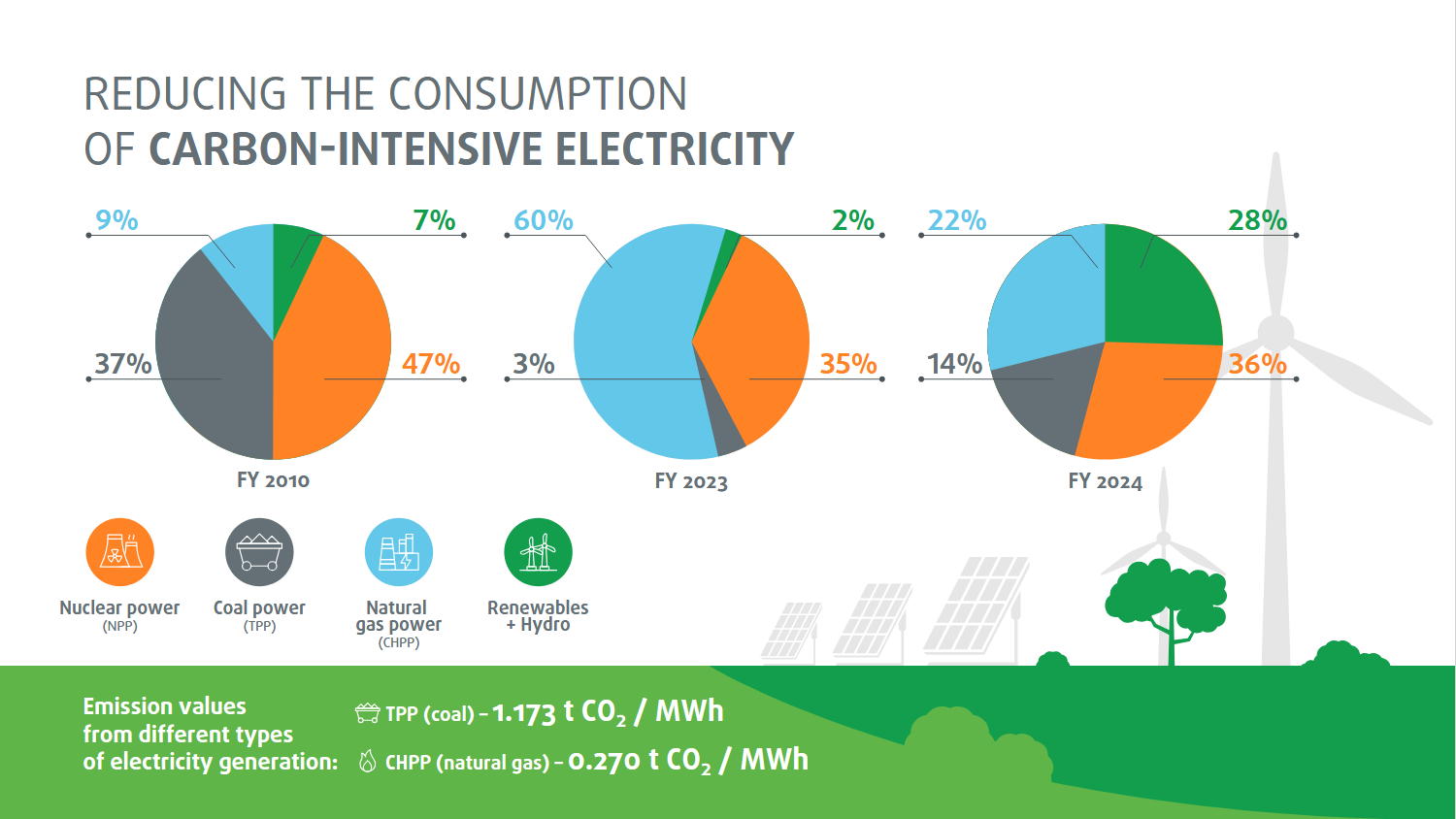
Source: interpipe.biz.
According to the company, the rate of reduction of Interpipe's carbon intensity is one of the highest in the industry, as it meets the European Green Deal goal of reducing emissions by 55% by 2030.
Plans for the next 5 years
According to Vladyslav Varnavsky, Interpipe's Director of Environment and Industrial Safety, the company has ambitious goals to further reduce greenhouse gas emissions.
By 2030, they aim to cut the carbon intensity of seamless pipe production by 26% and that of railway product manufacturing by 25%, compared to 2023 levels.
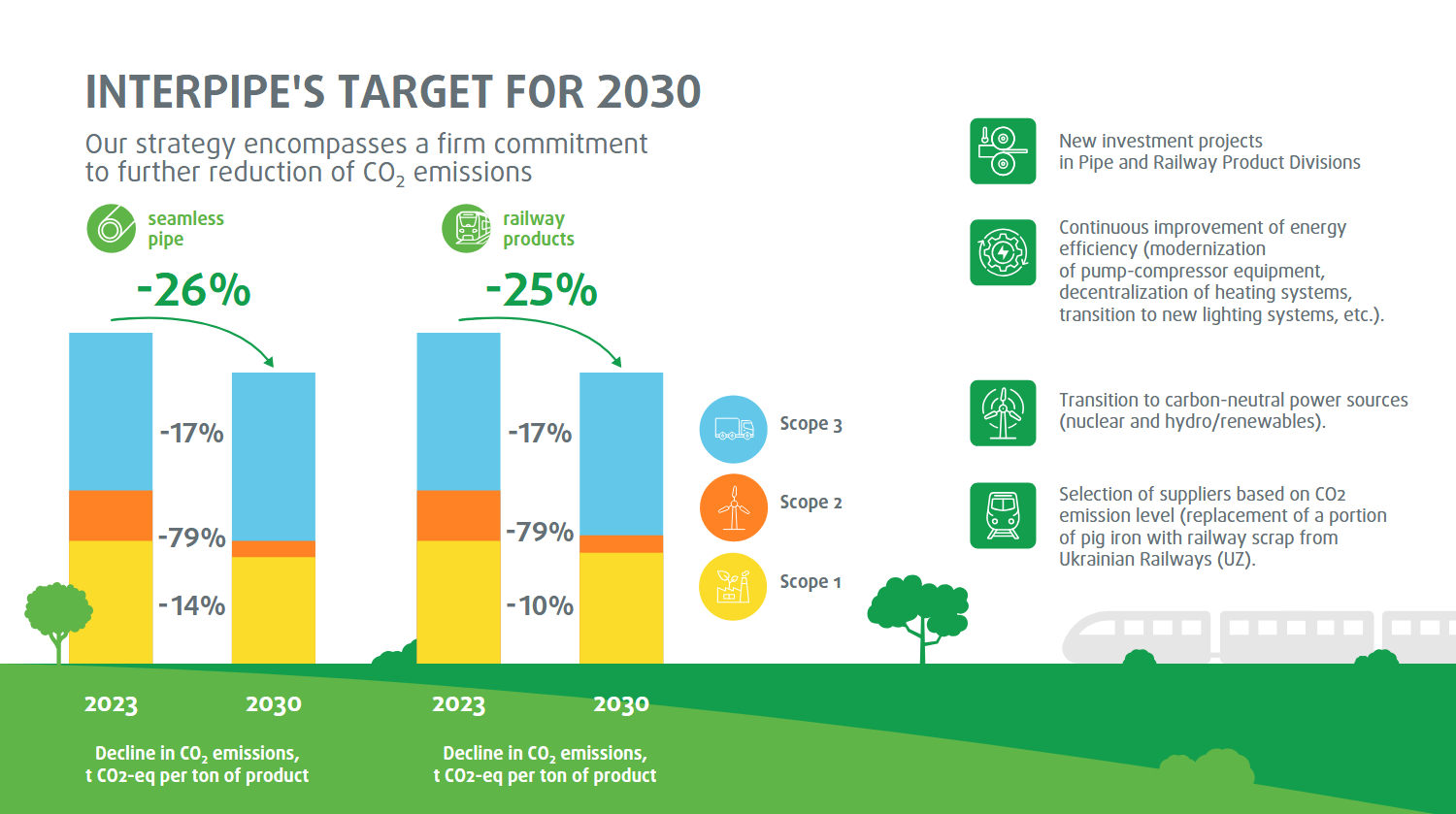
Source: interpipe.biz.
Further decarbonization will be implemented in the following areas
- implementation of new investment projects in the pipe and railway divisions;
- continuous improvement of energy efficiency;
- accelerating the transition to carbon-neutral electricity sources (nuclear + renewables);
- selecting green suppliers.
Dnipro Metallurgical Plant (DMZ)
On May 14, the company presented a comprehensive strategy for environmentally driven production upgrades aligned with the European Green Deal, including plans to construct renewable energy facilities.
The main stages of the unveiled strategy are:
- complete decommissioning of the company's coke production;
- construction of an electric arc steelmaking complex (EAF);
- transition to renewable energy sources.
The new EAF is already at the design stage.
According to Vitaliy Bash, CEO of DMZ, on May 13, the company completely shut down the coke production site. It is on its basis that they plan to build a solar power plant (SPP). DMZ plans to invest about $15 million in its construction.
Vitaliy Bash, CEO of DMZ, announced that the company fully ceased operations at its coke production site on May 13. The location is slated for the construction of a solar power plant, where DMZ plans to invest approximately $15 million.
The solar power plant will consist of double-sided solar panels with high efficiency. This modern equipment can convert both direct solar radiation and reflected solar radiation into electricity.
The planned area of the plant is about 40 hectares. The planned generation volume is expected to be about 40 GWh with an installed capacity of 30 MW.
As part of the new environmental strategy, the plant is considering upgrading the capacity of rolling shop No. 2 (mill 550) and using other types of green energy besides solar.
The company is confident that the construction of the EAF and other decarbonization measures will allow it to produce steel products which meet the environmental standards of the European Union and CBAM requirements.
Metinvest
Metinvest Group is preparing for a strategic step to phase out blast furnaces and replace them with electric arc furnaces. This will reduce CO2 emissions to the level currently considered the standard for green steel production in Europe.
In 2022-2023, the company's environmental expenditures amounted to $330 million, including $107 million in capital investments. Metinvest is reducing its carbon dioxide and other greenhouse gas emissions year after year. For example, in 2023, the company's Scope 1 CO2 emissions decreased by 19% year-on-year to 5.4 million tons, while its Scope 2 emissions decreased by 7% to 1.3 million tons.
At the same time, the intensity of direct CO2 emissions decreased by 6% to 2.3 tons of CO2 per ton of steel produced over the same period. This was mainly due to a more efficient energy balance of blast furnaces at Kametstal.
To reduce air emissions, Metinvest implemented environmental initiatives and modernized technologies at its enterprises. In particular, the Group overhauled coke oven batteries and took measures to improve efficiency at Kametstal, as well as to reduce emissions from blasting operations and stabilize the surface of dry tailings dumps at Ingulets Mining.
Use of solar energy
Metinvest also announced its intention to invest $18.1 million to equip its enterprises with solar power plants with a total capacity of 37 MW. It is planned that Central Mining and Kametstal will get their own solar power plants.
The expected annual savings due to the use of own electricity from solar panels are $4.9 million.
According to Metinvest's Chief Operating Officer Olexander Mironenko, solar generation will help reduce the carbon footprint of Metinvest's products, but not as much as equipment modernization and the transition to electric steelmaking.
The top manager says the company needs time to meet EU standards.
“Metinvest already uses up to 70% of green electricity, as the share of nuclear and renewable energy in the energy system structure has increased after the Russians destroyed almost all Ukrainian thermal power plants. However, we need time to modernize equipment and meet EU standards, so I would like to see Ukraine's CBAM obligations postponed for 3-5 years, taking into account the war,” he emphasized.
Mr. Myronenko also said that Metinvest plans to switch to electric steelmaking after the war is over. According to the company's estimates, it will take $8 billion and 7-8 years.
Ferrexpo
Mining company Ferrexpo aims to achieve zero emissions by 2050 and plans to invest $3.3 billion in production modernization to achieve this goal.
The company disclosed this amount in its Ferrexpo Climate Change Report in December 2022. These financial resources are necessary to achieve zero CO2 emissions. It is planned that approximately two-thirds of the investments will be allocated to the production and storage of renewable energy.
Interim results and plans for 2050
In 2023, Ferrexpo reduced the carbon intensity of its pellet production process (Scope 1 + 2) by 32% compared to the 2019 baseline. By 2030, the company intends to reduce the carbon intensity of its production by 50%. Ferrexpo aims to achieve zero emissions (Scope 1+2) by 2050.
Ferrexpo has identified the following projects as the key ones that will account for the bulk of its carbon emissions reduction
- switching to biofuels in the pelletizing process;
- gradual phase-out of fossil fuels;
- electrification of technological mining vehicles and equipment;
- use of hydrogen-fueled barges.
According to the company's estimates, these measures should provide 90% of the potential emission reductions and form the basis of its Net Zero strategy. The first three measures play a leading role, accounting for 82% of the emissions reduction.
The most effective emission reduction measure among the above is the transition to biofuels in pelletizing. Its implementation will require investments in the purchase of biofuels and integration of biofuel systems into production processes.
The company considers electrification of mining vehicles to be the fastest and easiest measure to implement. Ferrexpo will look for suppliers of electric vehicles suitable for ore mining and develop the infrastructure of charging stations for them.
However, the priority is to eliminate fossil fuels from the energy balance. The company says it has already begun planning a “green” transition.
The electrification of mining equipment and the use of hydrogen-powered barges can provide a smaller reduction in carbon emissions, but the company emphasizes that these measures remain important for the implementation of the Net Zero strategy.
ArcelorMittal Kryvyi Rih
Due to the war, the company curtailed its most ambitious strategic investment projects, but did not abandon its goal of transitioning to greener production. Thus, in 2022, a landmark event took place: the two oldest coke oven batteries No. 1 and 2 were decommissioned. The shutdown helped reduce emissions from coke production by 37%. New gas cleaning units were also installed in the BF Shop. In total, the measures taken that year resulted in an annual reduction in emissions by 35 thousand tons.
In 2023, ArcelorMittal Kryvyi Rih permanently shut down its sinter shop. This helped reduce pollutant emissions by 30 thousand tons per year.
In 2024, the company decommissioned the BF-7 at Blast Furnace Shop No. 1. Now almost 11 thousand tons of pollutants will not be released into the air annually.
After hot phase of the war is completed, ArcelorMittal Kryvyi Rih plans to engage international contractors to return to large-scale decarbonization projects.
The global company ArcelorMittal aims to reduce carbon emissions by 35% in Europe by 2030 and become completely carbon neutral by 2050.
Currently, the company has two technological paths for producing zero-carbon steel. The Smart Carbon pathway involves replacing coking coal with alternative carbon sources from biomass or agricultural waste. This waste is a source of carbon dioxide during its natural decomposition, so this energy can be classified as carbon neutral.
Another technology is the production of steel from scrap or direct reduced iron (DRI) in an electric arc furnace. DRI technology involves the direct reduction of iron from ore using natural gas, but at ArcelorMittal, natural gas has been partially replaced by hydrogen.
According to the GMK Center, a specialized agency, the total capital expenditure required to implement the already announced green steel projects in Ukraine is about $11 billion, or about $1,500 per ton of steel produced last year. These projects will only be implemented if Ukrainian companies have access to European green finance instruments similar to those received by European companies.
With European support, the Ukrainian steel industry will be able to decarbonize and meet the best European environmental standards. This requires coordinated efforts from all stakeholders: government, business and the public.